The Key to Digital Transformation in Manufacturing: Digital Thread
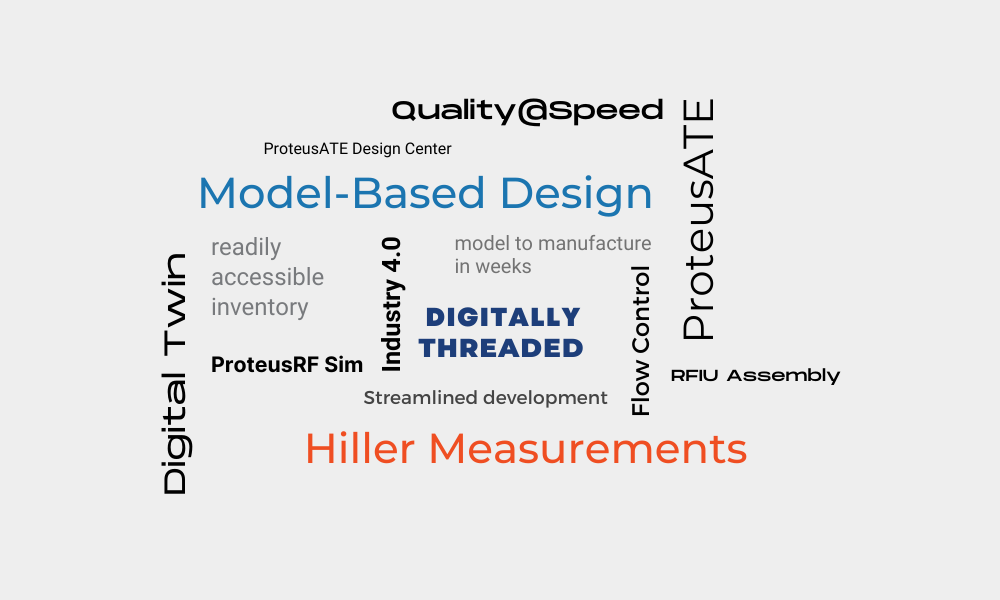
At Hiller Measurements, we’ve made distinct efforts to identify and mitigate waste in our design and manufacturing processes, and our greatest leaps have been with what we refer to as Digital Thread, the process of connecting formerly disparate value-added steps or processes through software, resulting in substantive reductions in cost and cycle times. It’s the way we’re re-thinking our business and truly creating meaningful change that benefits our customers.
Digital Thread is the process of connecting formerly disparate value-added steps or processes through software, resulting in substantive reductions in cost and cycle times – and it’s the way we’re re-thinking our business and truly creating meaningful change that benefits our customers.
Like many companies who have approached “digital transformation” with breathless grand plans, we began with a top-down, enterprise-level approach: major investments in PLM, long discussions on “Single Source of Truth” (to be discussed in a future blog), and man-months of investment leaving us with little success and much frustration. Often, it seemed we were reinforcing old methods with new tools, rather than making a true step-change in our abilities. Perhaps you’ve had similar experiences.
Going back to basics put us back on the right track.
How do you re-envision better processes if you don’t thoroughly understand that which you already have? We assumed we understood as an organization how work gets done. But when we put all stakeholders in a room and went through a structured value-stream mapping session, we realized we had much to learn. If you’re new to value-stream mapping, it is a technique to create a visual guide of all the components necessary to deliver a product or service, with the goal of analyzing and optimizing the entire process – you can read more about how to do this in Learning to See by Mike Rother and John Shook.
Having done this numerous times at this point, we recognized two axiomatic truths:
- How work gets done is often wildly at odds with what any stakeholder believes to be the case.
- The most significant ROI in process improvement is often not improving a value-adding step within a process. Rather, removing or minimizing the “waiting waste” where nothing is happening between value-adding steps brings the largest and most immediate benefit.
Discovering the Downfall of Waiting
If you haven’t yet done so, prepare to be shocked when you complete a present-state process map and a “Gemba walk” in your first value-stream session. You’ll likely find 80% or more of your schedule is consumed with non-value-added waiting waste.
Make the waiting waste go away, and you’ve increased your capacity by 500% without having to hire people or build buildings.
Recognizing these opportunities was revelatory for our team at Hiller.
Figuring out how to actually make that waiting waste go away is the fun part. It’s also referred to as the “future-state map” in value-stream talk. It was at this point where a meaningful vision for our transformation took shape. It’s true, we’ve developed new tools that re-define how we execute a value-added engineering process (designing a complex RF assembly for instance) utilizing a model-based paradigm as was discussed in the last blog. But more profound is how we used these tools to wholesale remove or minimize the waiting waste in our present state processes.
Let me give you an example:
Take the design of a cable assembly. Traditionally, there’s multiple, manually generated documents (work instructions, travelers, quality check lists, etc.) each created over the course of a full calendar day, and serially lined up, one needing to be done before the next can start.
To reduce waiting waste in cable assembly, we launched ProteusATE Cables and Harnesses (ProteusC&H), a model-based approach for cable/harness design and manufacture. With the ProteusC&H workflow, the once day-long documentation tasks have been replaced with a single model which in turn creates and delivers to each work cell all necessary manufacturing information. If the cable design changes, the associated downstream manufacturing data automatically updates. By connecting formerly manual steps with automated, model-based workflows, we made most documentation unnecessary, reduced cycle times, and minimized necessary labor.
Today, Hiller’s digital transformation is taking more of a “bottoms up” approach as we identify and attack waiting waste (and the other 6 forms of waste, or “muda” in Toyota-speak) in our day-to-day work with new tools and streamlined process tied together with digital thread. Taking this approach, we’ve brought meaningful results in relatively short order and have better informed ourselves of what our future, enterprise-level digital transformation will likely look like one day.